Rendering — the process of separating animal fats, usually by cooking, to produce usable ingredients such as lard, protein, feed products, or nutrients — is one of the best ways to convert poultry carcasses into other products. We are now able to reclaim or recycle nearly 100 percent of inedible raw poultry material, including bones and feathers, through rendering techniques.
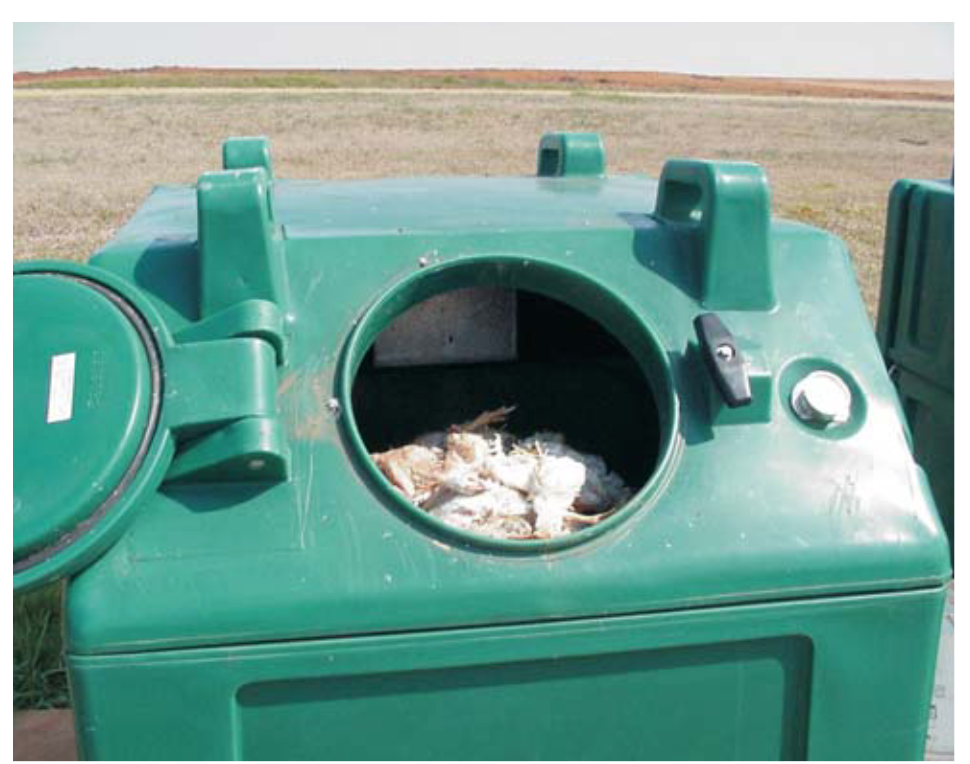
Historically, the animal protein in meat and bone meal residues was considered a waste of poultry processing; it was usually discarded, though it could sometimes be used as a fertilizer. Now rendering plants pick up or receive about 100 million pounds of waste annually to supply 85 percent of all fats and oils used in the United States. They also export 35 percent of the fats and oils used worldwide. Rendering operations provide a vital link between the feed industry and the poultry grower; they also help control odor and prevent air and water pollution.
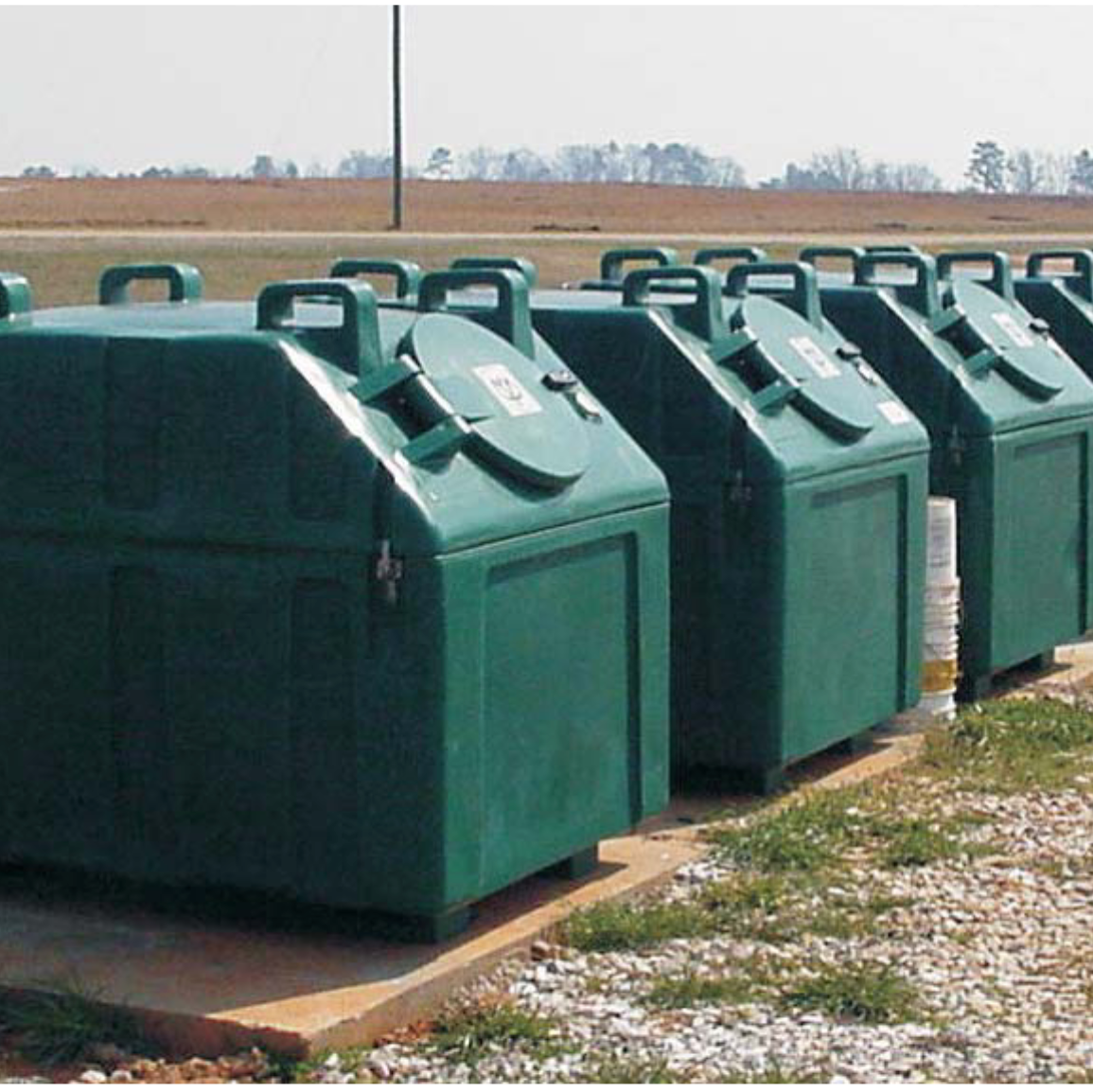
Rendering has not been widely practiced, however, as an on-farm method of poultry mortality management. Few rendering facilities are located in the production area and carcasses do not remain fresh long enough to be delivered long distances. Further, any transportation of the carcasses off-farm could spread avian diseases.
The converse of these difficulties is, however, rendering’s great advantage as a management technique; namely, it does remove mortalities from the farm and relieves the grower of environmental concerns related to other methods of disposal. Its potential economic benefit increases as more of the product is successfully recycled. Spurred by such considerations and concern to prevent further nutrient losses, growers and their industry partners are taking a second look at the rendering process.
Efforts to develop appropriate management and handling techniques to overcome obstacles associated with the routine pick up and delivery of carcasses to the rendering plant (especially the possible threat to avian health and the environment) have focused on long- and short-term alternatives to the immediate delivery of carcasses for processing. The earliest management adaptations relied heavily on daily pickups and refrigeration. Now, freezers that reduce the frequency of pickups are viable options as are other technologies that may be safer and more cost-effective including: acid preservation, grinding and fermentation, and extrusion.
Preparing for Immediate Delivery
Raw or fresh poultry mortalities that are destined for a rendering plant must be held in a leak-proof, fly-proof container; and they must be delivered to, or be picked up by, a rendering company within 24 hours of death. All mortalities must be held in a form that retards decomposition until they are collected.
Refrigeration
Some producers are experimenting with a technique that combines on-farm freezing or refrigeration and the rendering process to determine whether freezing can be an effective way for growers to preserve the dead birds until they can be rendered. Large custom-built or ordinary commercial freezer boxes are being used to preserve dead birds until they can be picked up and delivered to the rendering plant. Custom-built boxes or units are usually free-standing with self-contained refrigeration units designed to pro- vide temperatures between 10 and 20 °F.
Ideally, these freezer units will have no environmental or health impacts. The smaller ones are designed to allow the immediate removal of the carcasses from the grower; the larger ones, are to hold the birds frozen until the box is full or otherwise scheduled for delivery to the plant.
Large domestic freezers will hold about 250 to 300 pounds of dead birds. Specifically designed boxes can handle 1,600 to 2,000 pounds of dead birds and are easily loaded through various door arrangements. These units must also be sealed against weather and air leakage. Putting the birds in the freezer in a single layer and on a daily basis helps ensure that all the carcasses will be properly frozen. Fresh unfrozen carcasses are added to the top layer. Temperatures are set to freeze and should be regularly monitored to detect malfunctioning equipment; overloading is strongly dis- couraged as that can also inhibit the freezing process.
The freezers remain on the farm until the end of each growing cycle when they are emptied into a truck for transportation to the rendering facility. The refrigeration unit never leaves the farm, only the container holding the dead birds is removed or emptied.
Refrigeration is still an expensive option, though most of these units will last roughly 10 years and operate on energy-efficient circuit boxes with an operating cost of just a few dollars per day. Transfer of pathogens or harmful microorganisms between farms has not been found to be a problem with this method of collection. Although additional experience is needed to determine the effectiveness of this option, its proponents stress its usefulness as a way to reduce or eliminate potential pollution and improve conditions on the farm.
References
Blake, J.P., 1993. Mortality Management. Presentation. Poultry Waste Management and Water Quality Workshop. Southeastern Poultry and Egg Association, Atlanta, GA.
Zimmerman, M., 1993. Freezing for the Rendering Plant. Poultry Waste Management and Water Quality Workshop. Southeastern Poultry and Egg Association, Atlanta, GA.