Incineration of on-farm poultry mortalities increases in popularity as new technologies add affordability to perceived environmental and health advantages that incineration can offer over other methods of dead bird disposal. Engineering and technology research have developed several waste-to-energy options that are technically and environmentally sound. Litter, layer manure, and liquid waste can all be transformed into energy through one of several conversion technologies.
Combustion/Gasification
Most applicable to solid materials such as broiler or turkey litter, this burning process produces energy that can be used to heat air for space heating or crop drying or steam for heat and/or electricity. All of the phosphorus and potassium contained in the litter is conserved during the process, ending up in the ash, which has significant commercial value as fertilizer.
Combustion/gasification systems range in size from small farm units used for space heating and/or electricity to large-scale, centralized cogeneration systems that produce 10 to 40 megawatts of electricity (consuming 125,000 to 500,000 tons of litter per year). Large systems will probably require sophisticated scrubbers to keep nitrogen oxide emissions within regulatory limits; smaller systems may be exempt.
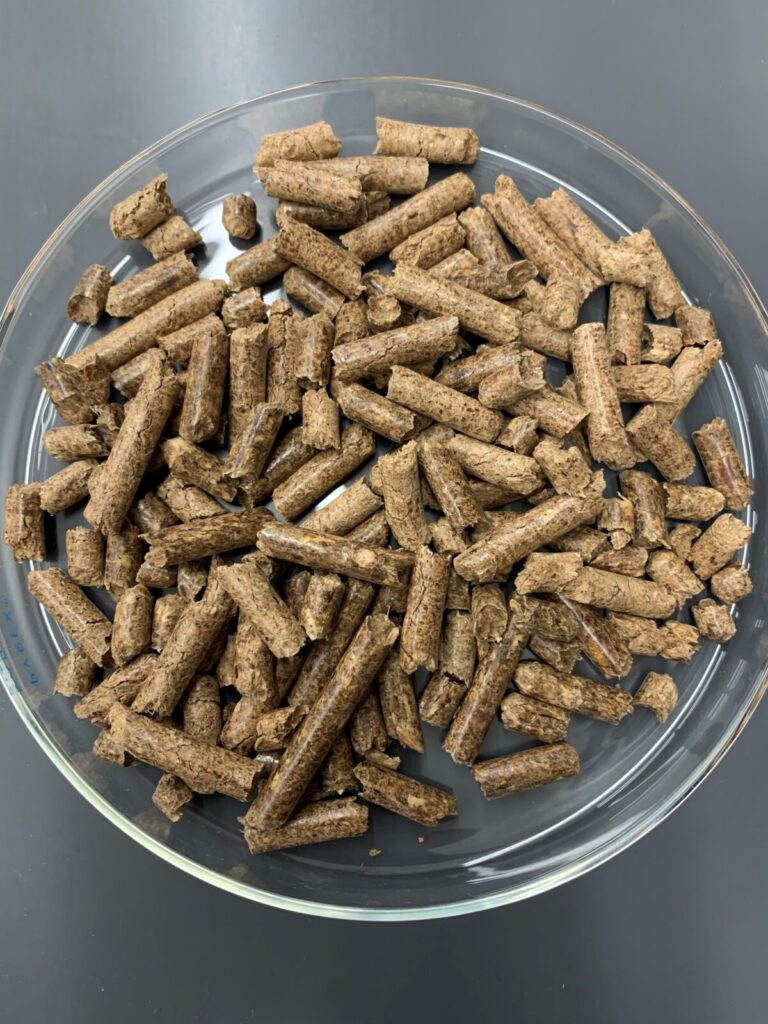

Densification
Poultry litter can be densified into pellets, cubes, or similar solid fuels. Densification facilitates storage, handling, transportation, and subsequent combustion (systems operate more efficiently when homogenous fuels are metered into the combustion chamber). Several litter pelletizing facilities are currently operating, but primarily for the horticultural or cattle feed markets, not as biomass fuels.
Although a portable or small-scale pelletizing system could be used on farms, the system has two primary drawbacks for poultry farmers:
- Litter must be dried to 8 to 10 percent moisture content prior to processing; thus a litter dryer (a large and expensive component) would have to be part of the densification system.
- Poultry litter is relatively abrasive and results in high equipment maintenance costs.
Anaerobic Digestion
This biological conversion process — in which microbes, in the absence of air, convert volatile organic constituents into biogas and water — is best suited to liquid or high-moisture materials such as layer manure or processing effluent. Biogas from digested manure is typically 55 to 85 percent methane and can be handled and used much like natural gas or propane, including for space heating and vehicle fuel. But biogas has problems:
- It’s more corrosive than natural gas or propane;
- Odor may be a problem, although much less than open lagoon systems; and
- It cannot be economically compressed or stored.
More effective microbes need to be identified, alternative system designs developed, and small- scale utilization systems made more cost-effective.
Enzymatic Conversion
This process uses enzymes to biologically transform cellulose materials into intermediary products that are then converted into liquid fuels and/or industrial feedstocks. As the conversion technology emerges as a technically and economically viable process, at least one company is planning to establish commercial facilities that may use poultry litter as a feedstock.
Cost-effective farm-scale systems are also being developed, promising considerable benefits to producers, including heating poultry houses from on-farm litter combustion.
Using Air-dried Litter as an Alternative Fuel
The first in a new breed of commercial electricity generating stations fueled by poultry litter was introduced in the United Kingdom in 1992. Today, the plant, which cost $30 million, has a gross output of 14.2 megawatts.
The plant is fired on about 143,300 tons of litter per year (roughly the same energy as would be derived from 66,139 tons of coal). Special road vehicles deliver the material to the plant’s storage bunker. The area of production is within a 31-mile radius of the plant.
Environmentally, this technology has a lot to offer:
- It creates demand for the product that effectively prevents the excessive application of litter on agricultural fields, thereby protecting water resources and restoring nutrient balance;
- Gases produced in the process are low in major pollutants and after treatment in a three-stage electrostatic precipitator are suitable for discharge to the atmosphere;
- It is low in cost and continuously available; and
- The ash by-product is high in potash and can be removed from the plant in bulk and used as a component of manufactured agricultural fertilizers.
Fluidized-bed Combustion
Fluidized, or bubbling, bed combustion has been used worldwide in industry for more than 20 years. Now some agricultural and government researchers and others in the poultry and waste management industries are probing the usefulness of burning poultry litter in a fluidized bed combustion system.
The objectives of modifying or otherwise developing this technology are to determine, first, whether this method can dispose of litter efficiently and cleanly, and second, whether this biomass is a suitable raw material for energy production.
Recent claims suggest that the technology has many applications:
- the generation of hot gases for heating and drying;
- the generation of electrical power;
- the generation of steam and pressurized systems to suit process inlet requirements.
If so adapted, it would have several advantages:
- modular designs that are inexpensive and easy to install;
- reduced power consumption to save operating costs;
- adaptability to a variety of waste streams should conditions change; and — of most importance to some poultry growers —
- ability to burn waste materials having an extremely high moisture content.
If these and other technologies for converting litter to energy are successful, they will help expand potential uses for litter, increase environmental well-being, and contribute to economic sustainability.
Poultry test burns were conducted at the Energy Institute of the Pennsylvania State University using fluidized bed technology. Researchers noticed in one test that using poultry litter actually reduced nitrous oxides from about 200 ppm to 100-150 ppm, probably because litter contains ammonia that reacts with nitrogen at high temperatures to form elemental nitrogen. Carbon dioxide emissions also decreased, in one test by about half. Three problems were overcome during the tests:
- Poultry litter plugged the feed tube: An air line was added down the center of the feed tube to assist the feed into the unit.
- Bed clinkering of the poultry litter was eliminated by the addition of clay;
- Fuel ash slag buildup in the upper part of the furnace was eliminated by adding overfire air. Following the tests, plans have been developed to build a 150-kilowatt-capacity modular power plant at a processing plant in Delaware.
Status of On-farm Litter-to-Energy Systems
Facing increasing pressure to dispose of surplus litter in environmentally friendly ways — and the fact that fuel for space heating is their greatest operating expense — broiler and turkey producers could benefit significantly by converting litter into heating fuel on-site. Assuming an average of 4,600 BTU per pound of litter and a 70 percent conversion system efficiency, 65 tons of surplus litter could provide about 86 percent of the thermal energy needed for a typical broiler house. Assuming a net economic value to the grower of $3 per ton of litter and an average propane cost of 75 cents/gallon, a farmer could net about $3,700 per year per house by using surplus litter as fuel.
Although no farm-scale litter-fired furnaces are yet available, several efforts are underway in 2004, most supported by U.S. Department of Energy funds. To be commercially successful, such systems must be technically viable, economically feasible, and user-friendly. In addition to handling the litter in a trouble-free manner, the system must be able to manage ashes produced and meet government regulations for emissions and other environmental concerns.
Given the challenges of developing workable on-farm litter-to-energy systems, large-scale, centralized systems may be the answer for at least the present, or until farm-scale systems become commercially available. Large-scale systems can address environmental concerns associated with traditional management of surplus littler and may economically benefit participating producers. Perhaps most important, given the regulatory climate, these systems relieve producers of responsibility (and liability) for surplus litter management.
References
Dagnall, S.P. 1992. Poultry Litter as Fuel in the UK — A Review. Proceedings of the Incineration Conference, Albuquerque, NM.
Environmental Framework and Implementation Strategy for Poultry Operations. 1998. A Voluntary Program Developed and Adopted by the Poultry Industry at the Dec. 8-9, 1998 Meeting of the Poultry Industry Environmental Dialogue.
Moulton, B.W., R.T. Wincek, and B.G. Miller. 2000. Evaluation of the Combustion Performance of Poultry Litter in a Bubbling Fluidized Bed Combustor. Center for Fuel Utilization, The Energy Institute, The Pennsylvania State University.
Vir, M.J. On-farm Energy Generation from Broiler Litter. Spinheat Ltd., 1222 Bronson Road, Fairfield, CT. Unpublished paper.
Vayda, S. 1996. Marketing Package Addressed to the Poultry Water Quality Consortium. Vayda Energy Associates, Inc., Hampstead, MD.
Wimberly, J. 2002. The Status of On-farm Litter-to-Energy Systems in the United States. Proceedings National Poultry Waste Management Symposium, Birmingham, AL. ISBN 0-9627682-6-8. National Poultry Waste Management Symposium Committee.