Manure management on duck, geese, and some layer operations is often handled through liquid waste systems, even though water increases the volume of waste to be processed. In liquid waste management systems, collection and storage are generally combined in one operation, in facilities that may include pits, settling tanks, and/or lagoons (earthen storage ponds). Lagoons are unique in that they are the only manure storage systems that have a treatment volume incorporated into their design and management. Additional treatment may sometimes be used to convert liquid waste’s nutrient and mineral content into more stable products.
Commercial layer operations involve a variety of housing and manure handling practices which can produce different magnitudes of an environmental footprint. In cage layer systems today, the houses are commonly either high-rise (HR) or manure belt (MB) style (Figure 1(a) and (b), respectively. However, in the southern U.S., lagoon systems are still found on many older operations (Figure 2). Liquid waste management systems can be easier to automate and are less labor intensive than dry waste systems. However, constraints on the management system appear to be greater when the system is liquid:
- the lagoon or holding facility must be drawn down when filled – the grower has less flexibility for scheduling land applications,
- unless properly designed and sealed, the contents of the waste storage structure may leach into groundwater or overflow into ditches, agricultural drains, or other surface water resources,
- toxic gases and/or unpleasant odors can occur with liquid waste, particularly when it is agitated or stirred,
- flies may be a problem if the lagoon is mismanaged or forms a mat on top, and
- nearly all states now have clean water laws that prohibit wastewater discharges to surface waters or groundwater recharge areas. Therefore, nearly all animal operations with a liquid waste management system must have permits to comply with state laws, even if they are not required to file for federal National Pollution Elimination Discharge System (NPEDS) permits.
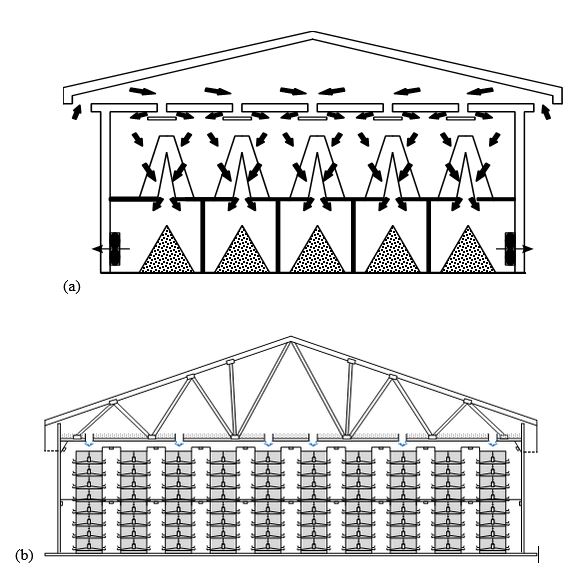
In contrast, dry waste systems are perceived to have less environmental risk but are more difficult to automate and are more labor intensive.
Liquid Collection Methods – Pit Storage
Layers and pullets are often raised in cages arranged in rows or decks. Manure falls directly into a pit or is scraped into the pit from dropping boards. Pits must be cleaned regularly, and the manure stored, or land applied. Ventilation fans are necessary to dry the manure, remove toxic gases, and reduce fly problems and offensive odors. (A lagoon may also be present, particularly in the southeastern U.S., to treat the waste before land application). There are three basic pit designs:
Shallow-pit Systems
Built of concrete at ground level, are 4 to 8 inches deep and located 3 to 6 feet below the cages. Manure is scraped from the pit or flushed out with water and collected in a storage area or lagoon or loaded directly into a manure spreader.
Deep-pit Systems
Usually 4 to 8 feet wide and may extend 2 to 6 feet below ground level with the cages at least 8 feet above the concrete or masonry floor of the pit. The pit floor and sidewalls must be sealed and thoroughly protected from stormwater runoff and groundwater seepage. Foundation drains and external grading are needed to remove subsurface water and to drain surface water away from the building.
High-rise Systems
Similar to deep-pit systems but are built entirely aboveground. The cages are 15 to 30 feet above the ground. The pit floor should be concrete and graded, with foundation drains. The water supply must be controlled if the wastes are retained in place for extended periods. If outside water penetrates the system, the manure can develop a serious fly problem or perhaps leach nutrients to groundwater.
Again, in cage layer systems today, the houses are commonly either HR or MB style. Approximate partitioning of the total cage layer houses in the U.S. today is 70 percent HR and 30 percent MB, although new houses typically incorporate the MB style.
In HR systems, manure either drops into a storage area beneath the cages or first falls onto dropping boards, that are periodically scraped (four to six times daily), dropping the manure into storage below the cages. In each system, manure drying, for the most part, is done via ventilation air while in storage. Warm ventilation air passes through the hen and cage area and is directed to flow over the manure surface, providing some level of drying. The ventilation system prevents most of the ammonia in the manure storage level from rising to the hen level by maintaining a pressure gradient between the two levels that improves bird-level air quality. The lower-level manure storage area typically has space to store manure for up to a year, although some operations remove the manure more frequently.
In MB housing, fresh manure (~75 percent moisture content) drops onto a belt beneath each cage row. Manure on the belt dries naturally through normal ventilation or a forced air stream is directed under the cages through an air duct over the manure surface to assist drying. Manure is conveyed via the belts under the cages to one end of the house where another belt carries it outside for removal to an on-farm or, perhaps, off-farm storage or composting facility or possibly directly to land application. Depending on the system, manure removal may occur on a daily, semi-weekly, or weekly basis.
Settling Tanks
Concrete, concrete block, or steel storage tanks may be used to collect solids and to skim floating material from a layer operation. A floating baffle or other separator can be installed to remove eggshells, feathers, and other debris. The tank should be placed between the layer house and the storage lagoon. Normally, a settling tank is four feet at the deep end, sloping to ground level. Walls are slotted to allow drainage for the settled waste.
It is recommended that two settling tanks be installed; one can be drained and cleaned while the other remains in operation. Tanks must be properly constructed and sealed to prevent groundwater or surface water pollution. Tanks and lagoons may generate dangerous gases and unpleasant odors and may require protective measures.
Treatment Lagoons
Lagoon systems handle highly diluted manure (96 percent or more water) that can be pumped through irrigation systems. Properly designed and managed anaerobic lagoon treatment systems should have less than one percent solids, typically from 0.1 to 0.5 percent solids. Lagoons also have a manure treatment function. They use anaerobic and aerobic bacteria to decompose the waste and can be used as digesters to convert large masses of waste into gases, liquids, and sludge. Livestock lagoons are small-scale waste treatment plants containing manure that is usually diluted with water and rainfall. Dilution water controls ammonia and salt concentrations, so that bacteria can function properly. Lagoons are designed to enhance microbial digestion of organic matter and volatilization of nitrogen compounds, thereby reducing the land area requirements for disposal by 50 to 75 percent.
Lagoons are relatively easy to manage, convenient, and cost-efficient. Storage and land application can be handled more opportunely, and labor and operating costs are minimal after the initial investment for lagoon construction. These facilities became a popular component of waste management systems during the 1970s when interest shifted from using waste as fertilizer in land applications to treating waste to produce a more convenient waste management system overall (with less organic content to apply). Lagoons are still a common sight on many layer and swine operations in the southeastern U.S.
The decomposition process will be both aerobic (requires oxygen) and anaerobic (without oxygen). Anaerobic bacteria in animal waste cannot work in the presence of oxygen. In contrast, aerobic bacteria must have oxygen to survive; therefore, anaerobic lagoons are deep and airless while aerobic lagoons are shallow, spread over a large area, take in oxygen from the air, and support algae growth. Both aerobic and anaerobic lagoons provide storage and disposal flexibility. However, anaerobic lagoons are much more common.
Anaerobic lagoons can be a source of odors and nitrogen losses and may require frequent sludge removal if they are undersized. Groundwater protection may be difficult to secure for any lagoon unless constructed properly or a liner is installed. If mechanical aeration is used for an aerobic lagoon, energy costs should be included in the operating expenses. Regardless of lagoon type, proper management is critical for lagoon maintenance and operation.
Aerobic Lagoons
The design, shape, size, capacity, location, and construction of a lagoon depends on its type. Aerobic lagoons are not a practical solution to most waste management problems because they require too much surface area to maintain sufficient dissolved oxygen. An aerobic lagoon may require 25 times more surface area and 10 times more volume than an anaerobic lagoon. However, despite the expense, some growers may consider an aerobic lagoon, particularly if they are in an area where odor is a sensitive issue.
Some of the sizing issues can be solved by mechanical aeration – pumping air into the lagoon – but energy costs associated with continuous aeration can be problematic. To their credit, aerobic lagoons will have better odor control, and the bacterial digestion associated with aerobic lagoons will be more complete than digestion in anaerobic lagoons.
Lagoon design and loading specifications should be carefully followed and monitored to increase the effectiveness of the treatment. No more than 44 pounds of biological oxygen demand (BOD) should be added to the lagoon per day per acre. The lagoon should have sufficient depth so that light will penetrate the three to four feet of water. Effluent from the lagoon should be land applied to avoid long-term ponding and to make economical use of the nutrients that remain.
Anaerobic Lagoons
Anaerobic treatment lagoons are earthen basins containing diluted manure that will be broken down or decomposed without free oxygen. In the process, the organic components or BOD in the manure will be liquified or degraded naturally. Anaerobic lagoons must be properly designed, sized, and managed to be an acceptable animal waste treatment facility. Liquid volume rather than area determines the size of anaerobic lagoons. The lagoon should accommodate the design treatment liquid capacity and the amount of wastewater to be treated. It should also have additional storage room for sludge buildup, temporary storage room for rain and wastewater inputs, extra surface storage for a 25-year, 24-hour storm event, and at least an additional foot of freeboard to prevent overflows.
Nutrient concentrations in all properly working anaerobic lagoons are low because of the high volume of dilution water, nutrient settling, and NH3 volatilization. During storage and treatment, N and P are reduced in concentration. The P tends to settle to the bottom and accumulate in the sludge which is infrequently (if ever) removed. An estimated 80 to 90 percent of the P produced by the animals will be retained in the sludge. The N is lost from the lagoon surface as NH3 and other N gas. N loss can range from 30 to 80 percent depending on temperature, storage duration, and pH. As a result, lagoon effluent contains a relatively small amount of N.
An estimated 95 percent of the potassium produced by the animals will remain in solution and be removed annually when the effluent is land applied. An anaerobic lagoon in proper balance will have a pH ranging from 7 to 8 (slightly basic). The pH in new lagoons without adequate dilution water or in overloaded lagoons may be 6.5 or less, which will create odor problems. N losses will be greater in warm weather.
The design criteria for anaerobic lagoons are based on the amount of volatile solids to be loaded each day. The range is from 2.8 to 7.0 pounds of volatile solids per day per 1,000 cubic feet of lagoon liquid. The amount of rain that would collect in a 25-year, 24-hour storm event requires at least 5 to 9 inches of surface storage, although the actual volume of surface storage required is site specific.
To protect the groundwater supply, lagoons should not be situated on permeable soils that will not seal, on shallow soils, or over fractured rock or karst topography. The bottom of the lagoon must not be below the water table. Mortalities must not be disposed of in lagoons. Screening the wastes before they enter the lagoon helps ensure complete digestion and the quality of wastewaters for land application.
Lagoons work best when they are loaded continuously. Therefore, a waste management system should be utilized that loads the lagoon at least weekly, and preferably daily. Infrequent shock overloading can result in sharp increases in odor production and wide fluctuations in nutrient content. Lagoons should be filled with water to one-third to one-half of the design volume before manure is introduced into the lagoon. This will ensure sufficient dilution water is available for the establishment of bacterial activity and minimize start-up odors.
Starting a new lagoon in late spring/early summer is best and will allow establishment of a bacterial population before cold weather and help prevent excessive odors the following spring. Generally, the bottom liner of most lagoons is compacted earth. Some type of clay is the preferred material. Materials such as bentonite can be added to soil to improve the acceptability of soil for liner material. If the soil type is inappropriate, then an impervious liner may need to be added (plastic, concrete, etc.).
Drawdown of lagoon liquid can be used for land applications guided by regular nutrient management planning and sampling of the lagoon liquids and soils to ensure safe and effective applications. When sludge accumulation diminishes the lagoon’s treatment capacity, it too, can be land applied under strictly monitored conditions. Secondary lagoons may be needed for storage from the primary lagoon. Using a secondary lagoon for irrigation also bypasses some of the solids picked up in the primary lagoon.
Information and technical assistance and possible cost share programs are available for producers who determine that a lagoon system should be part of their nutrient management plan. The USDA Natural Resources Conservation Service (NRCS) and the Cooperative State Research, Extension, and Education Service offices can provide additional assistance. Local county Extension offices can also offer information and assistance.
Land Applications
Land application of liquid waste can be achieved with a manure slurry or irrigation system. If application is applied directly on the crop, care must be taken to prevent ammonium toxicity and burning the crop. Raw layer manure contains high amounts of uric acid and should be thoroughly mixed before application. Layer lagoon sludge is denser than pullet lagoon sludge because of its higher grit or limestone content and may need to be diluted before application.
Timing is a major factor in successful land application of manure. There should be no land application prior to, during, or immediately following a rainfall event. In addition, manure must be uniformly applied – whether using a manure spreader or an irrigation system. It is critical, particularly during a drought, not to coat the forage/plants with lagoon liquid. Several small applications of lagoon effluent are better than one large application.
Lagoon effluent is primarily disposed of by land application. Proper spreading on the land is an environmentally acceptable method of managing waste. However, because of increasing environmental concerns and the need to match closely the fertilizer needs of the crop with the nutrient values in the soil and manure, farmers can no longer simply spread manure. Soil samples and manure nutrient analyses are critical to environmentally sound waste management programs today.
The USDA, NRCS, Cooperative State Research, Extension, and Education Service, and other agencies offer poultry waste and nutrient management planning assistance. These organizations have worksheets to help growers plan liquid waste management, which includes the following tasks:
- determining the amount and volume of waste generated,
- calculating land application requirements,
- sampling and analyzing the nutrient composition of poultry litter, manure, slurry, or sludge, and
- matching the nutrients available in the materials with crop nutrient requirements for land application.
Detailed information on how to prepare nutrient assessments, conduct soil sampling, read a laboratory nutrient analysis, and calculate application rates, timing, and methods of application are available from these agencies or the local county Extension office. Use of proper nutrient planning will assist growers in making economical, practical, and environmentally safe use of the organic resources generated on their farms.
References
Barker, J. C. 1996. Lagoon design and management for livestock waste treatment and storage. North Carolina Cooperative Extension Service Publ. No. EBAE 103-83. North Carolina State University – Raleigh.
Bodman, G. R. 1996. Lagoons for management of livestock manure. University of Nebraska Cooperative Extension Publ. No. EC96-779-C. University of Nebraska – Lincoln.
Fulhage, C., and D. Pfost. 2007. Swine manure management systems in Missouri. University of Missouri Extension Publ. No. EQ 350. University of Missouri-Columbia.
Hamilton, D. W., B. Fathepure, C. D. Fulhage, W. Clarkson, and J. Lalman. 2006. Treatment lagoons for animal agriculture. In: Animal Agriculture and the Environment: National Center for Manure and Animal Waste Management White Papers. J.M. Rice, D. F. Caldwell, and F. J. Humenik, (eds), pp 547-574. Publ. No. 913C0306. ASABE. St. Joseph, MI.
Lorimor, J., W. Powers, and A. Sutton. 2004. Manure characteristics. MidWest Plan Service Manure Management Systems Series. MWPS-18 Section 1. Available at: https://www.canr.msu.edu/uploads/files/ManureCharacteristicsMWPS-18_1.pdf. Accessed: 24 February 2021.
Pfost, D. L., C. D. Fulhage, and D. Rastorfer. 2000. Anaerobic lagoons for storage/treatment of livestock manure. University of Missouri Extension Publ. No. EQ 387. University of Missouri-Columbia.
VanDevender, K. 2011. Liquid manure solids management. University of Arkansas Cooperative Extension Service Publ. No. FSA1041. November.
Xin, H., R. S. Gates, A. R. Green, F. M. Mitloehner, P. A. Moore, Jr., and C. M. Wathes. 2011. Environmental impacts and sustainability of egg production systems. Poult. Sci. 90:263-277.
Figure 1. Schematic representation of high-rise layer house (a) and manure belt layer house (b)1.