Mortality management is an important responsibility for contract poultry producers. The exact number of daily mortalities will vary depending on the number of birds on the farm as well as their size and age. Because mortality losses constitute a relatively large portion of the total wastes generated in poultry production, their disposal must be managed in a biologically secure, environmentally safe, and cost-effective manner by the grower. As part of a typical broiler, breeder, pullet, and commercial layer contract, the grower is responsible for disposing of all mortality in a manner that complies with local, state, and federal regulations and meets the standards and expectations of the integrator or contracting poultry company (Brothers and Stanford, 2022).
Growers have several choices when it comes to a mortality disposal method and how they apply the chosen method to their unique farming operation, keeping in mind there are advantages and disadvantages to every system. Mass die-offs such as in the case of a highly pathogenic avian influenza outbreak or catastrophic losses caused by a power failure or severe storm damage create additional challenges. Mass mortalities in large numbers quickly overwhelm daily mortality methods and often require outside assistance to manage. Growers should carefully consider the trade-offs of each option – the differences in resource requirements and outcomes involved in each mortality management practice – and the effect of local conditions and personal preferences to determine the method of mortality management that best meets their needs. Common mortality management options include 1) composters, 2) incinerators, and 3) freezers. Dehydrators are a relatively new option that has recently appeared on the market in some states.
Composting
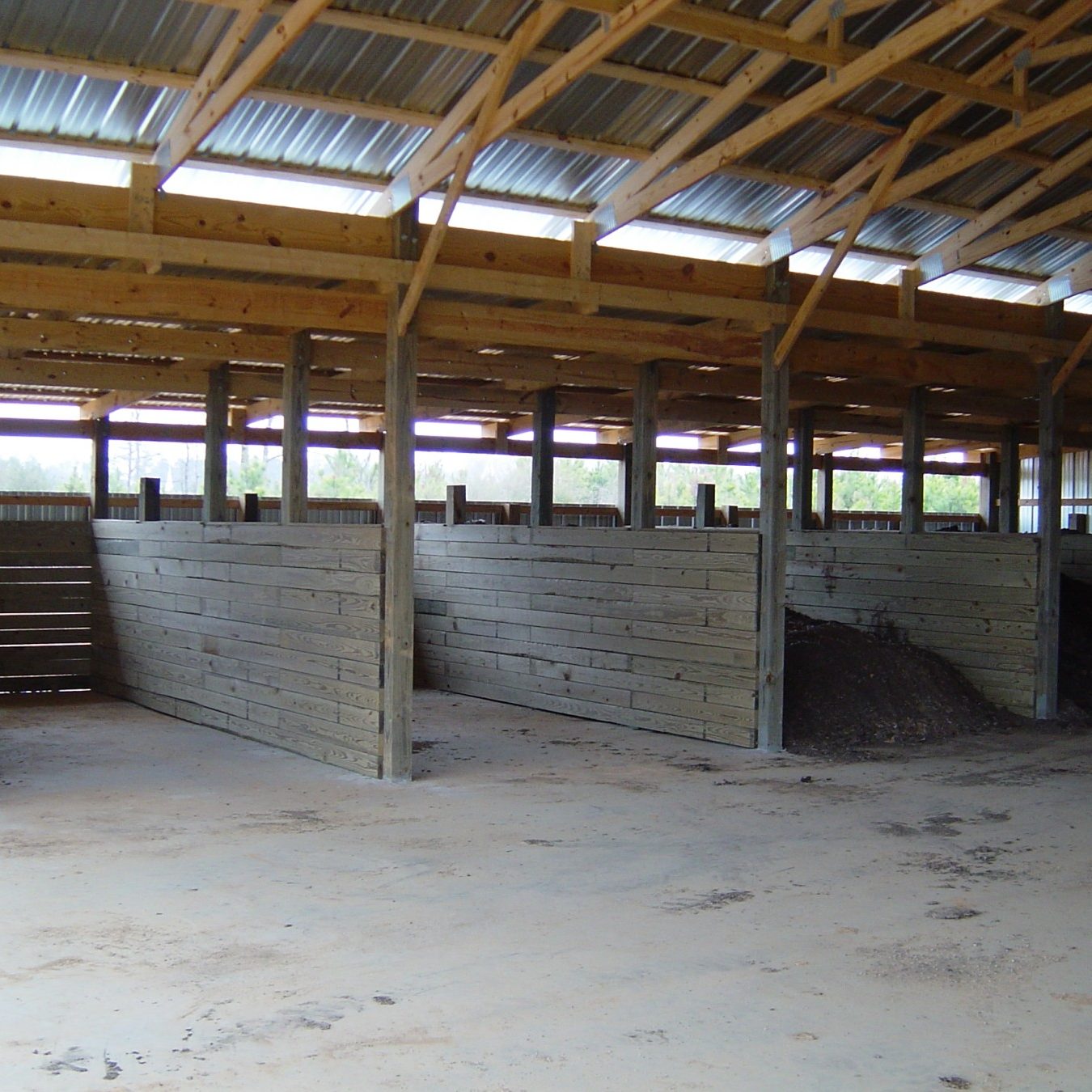
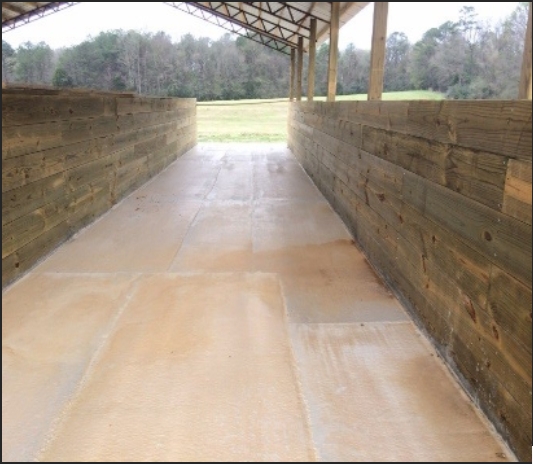
Composting is the most widespread method for the proper and complete decomposition of poultry carcasses. Most people are somewhat familiar with the general idea of composting, which is defined as the biological decomposition and stabilization of organic matter under controlled conditions. It is an aerobic process (requires oxygen) carried out by microorganisms that metabolize organic waste (poultry carcasses) as an energy source.
The two most common composting methods on poultry farms are
- Bin/alleyway composters
- Rotary drum composters
Bin (Figure 1) or alleyway (Figure 2) composters are similar in construction, having 1) concrete floors, 2) sidewalls to contain compost material, and 3) a roof to prevent rainfall entry. Well-constructed bin and alleyway composters will last many years with minimal maintenance, making the long-term cost of these composters low. Used poultry litter is often the primary composting or “bulking” material used along with mortality in alternating layers to fill a compost bin or alleyway and the material is then left to decompose over time. Composters are often built as part of a dry-stack litter shed but can be stand-alone structures. Composting is a recipe, and it requires the proper:
- Moisture content (40-60%)
- Carbon to nitrogen (C:N) ratio (25-35:1)
- Oxygen level (> 5%; 10-20% is better)
- Level of carbon source or bulking material (use enough)
- Mortality (don’t use too much and overwhelm the system)
If one or more of these ingredients is out of balance, you will have issues maintaining adequate temperature and achieving efficient composting. Attention to management is essential for success. Failure to properly manage the system will create odors and flies and attract unwanted scavengers and other vermin to the site. Proper management is vital to avoid nuisance complaints. Orderly loading of ingredients is critical for efficient compost activity. Regardless of type, ingredients should be layered into the composter as illustrated in Figures 3 and 4.
- Place an initial layer of 8–12 inches of fresh litter on the concrete slab floor. This litter will supply bacteria to start the process and will also help absorb carcass fluids or excess water that may be added to the composter.
- Next, add a layer of bird carcasses. Arrange carcasses in a single layer side by side, touching each other. Place carcasses no closer than 6 inches to the walls of the compost bin. Carcasses placed too near the walls will not compost as rapidly because of lower temperatures there and may cause odorous liquids to seep from the compost.
- Next, add a layer of litter. This layer should be twice as thick (8–10 inches) as the layer of carcasses underneath. If only a partial layer of birds is needed for a day’s mortality, the portion used must still be covered with litter. The rest of that layer can be used with subsequent mortality in the coming days.
- After completing the initial layer, add subsequent layers of carcasses and litter/bulking material until a height not exceeding 5–6 feet is reached. The top layer will be a cap of 8–10 inches of litter. A height of 5–6 feet with adequate porosity and moisture levels is not a fire hazard. Keep in mind, however, the potential for spontaneous combustion, and monitor temperatures throughout the composting process. Excessive height can induce higher compost temperatures that exceed 170°F and increase the chance of spontaneous combustion. Additional carbon/bulking material may need to be added to better facilitate the decomposition process with birds larger than 8.5 pounds.
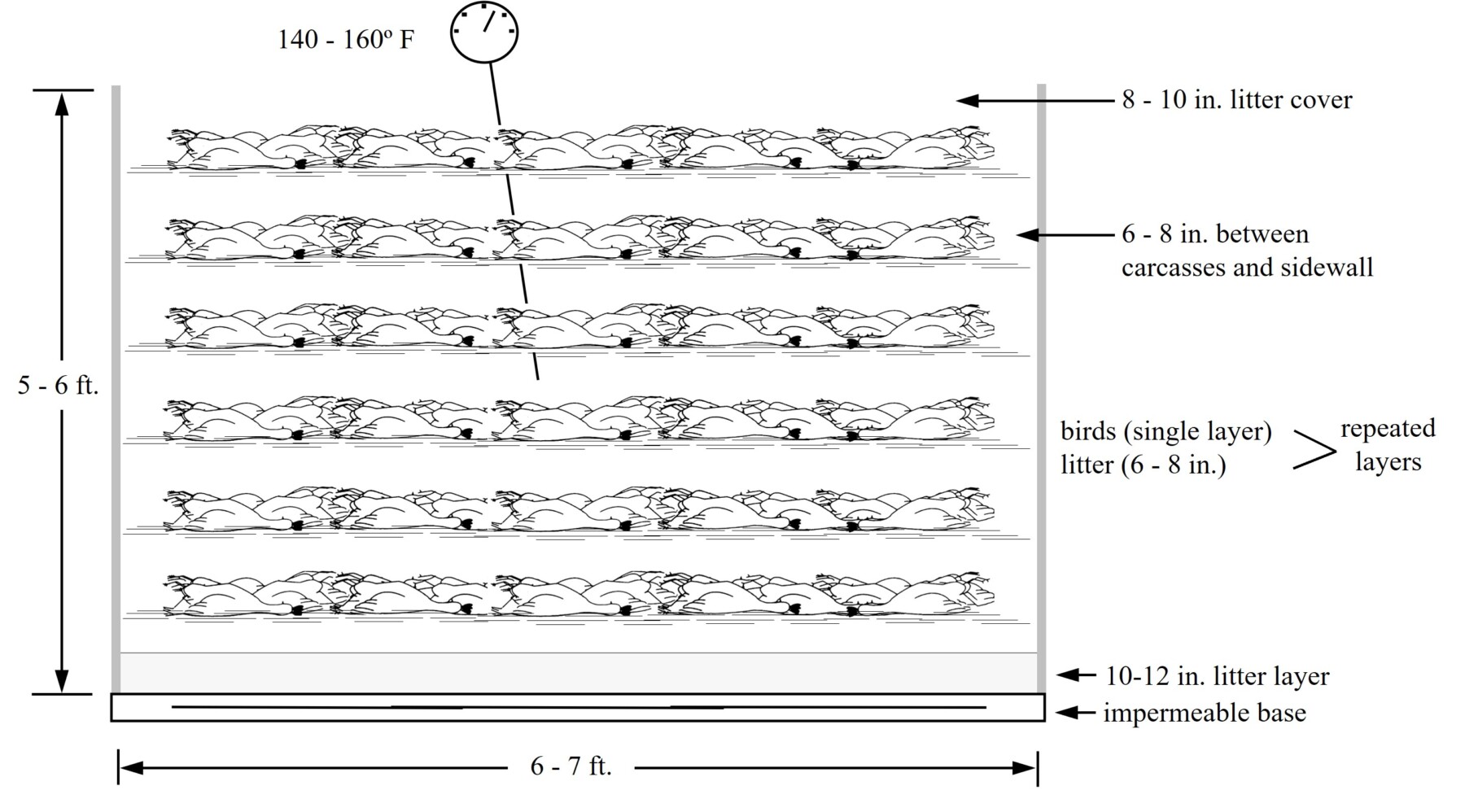
- In-vessel or rotary drum composters (Figure 5) are the latest innovations in composter technology. These systems use controlled air infusion and simplified aeration techniques to decrease the time and daily management needed to compost material. However, the same principles apply as with bin/alleyway composting, and proper management is critical to success.
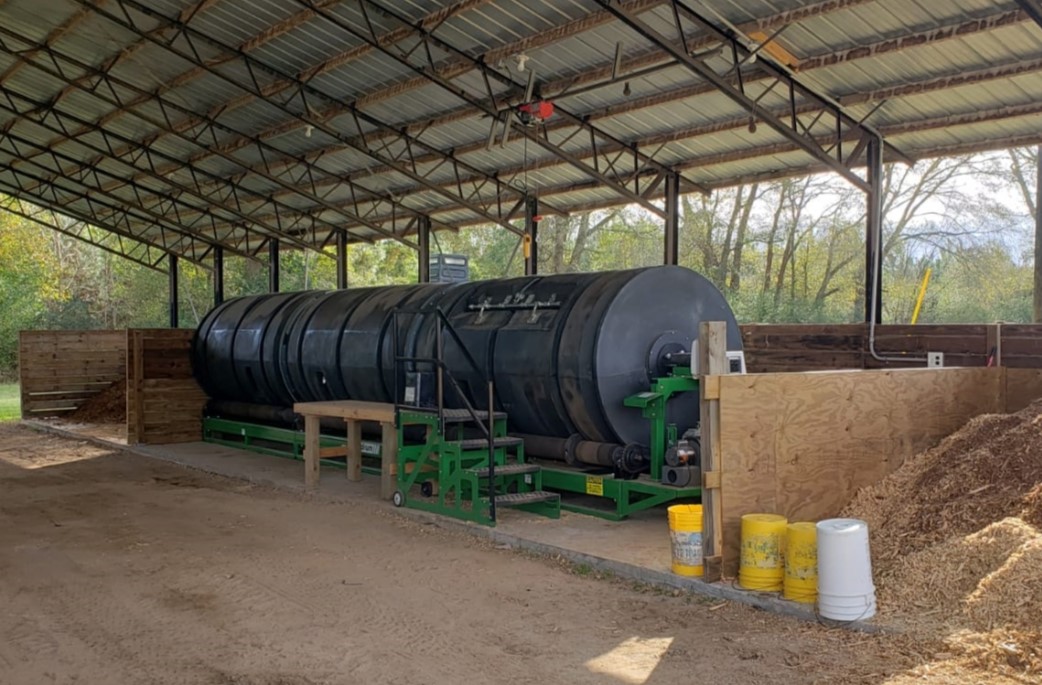
Proper composting is part art and part science and is essential to the grower for disease management, neighbor relations, and regulatory reasons. Composting is a forgiving process. Meaning that, if you mess it up, given some time, you can fix it. Most growers fail because they get the material too wet. Mixing additional bulking material in compost that is too wet will balance the moisture content and allow the process to continue working. Material that is too wet is often anaerobic and will produce little heat, but lots of odor and flies. A properly managed composter produces high temperatures (130-140°F), minimal odor, and few flies. Neighbor relations are an important part of poultry farming and spreading improperly composted material onto row crop fields and pastures can have far-reaching negative consequences. For the sake of the farm and the poultry industry, every grower should strive to maintain a good neighbor policy by doing the right things. Static bin composters with both primary and secondary bins are more labor-intensive because, once a smaller primary bin is full, it needs to sit for roughly 2 weeks. During this time, microbes break down roughly half the carcass material. However, they eventually run short of oxygen and the material must be turned into the secondary bin for the process to be completed. After 2 weeks in the secondary bin, carcass material will be decomposed if temperature and moisture levels are correct. Therefore, it may take 5–8 weeks or more from the time you start to fill a bin until you have finished composting. Once finished, the compost material is ready to spread as a soil amendment, similar to chicken litter. Table 1 provides a troubleshooting guide for composting poultry carcasses.
Table 1. Troubleshooting guide for poultry carcass composting
Problem/ Symptom | Probable Cause | Suggestions |
---|---|---|
Improper Temperature | Too dry (< 40% moisture) Too wet (> 60% moisture) Improper C:N ratio Improper mixing of ingredients Adverse environment | Add water Add Bulking material and Turn Evaluate & adjust bulking material Layer ingredients properly Ensure adequate cover over top |
Failure to decopose | Improper C:N ratio Carcasses layered too thickly Carcasses too close to outside edge | Evaluate & adjust bulking material Single layer the carcasses Maintain minimum of 6” between carcasses and outside edges |
Odor | Too wet Too low C:N ratio Inadequate cover between layers and on top | Add bulking material and turn Evaluate & adjust bulking material Use 6 to 8” of cover between layers and 10 to 12” over the top |
Flies | Too wet Poor sanitation conditions Failure to reach proper temperature Inadequate cover between layers and on top | Add bulking material and turn Avoid leaching from pile Assess C:N ratio; layer properly Use 6 to 8” of cover between layers and 10 to 12” over the top |
Scavenging animals | Inadequate cover over carcasses | Use 6 to 8” of cover between layers and 10 to 12” over the top Avoid initial entry with fence or barrier |
Rotary Drum (or In-Vessel) Composting
In-vessel composting is usually done in an enclosure, such as a large-diameter drum. The material is typically agitated, turned, and/or force-aerated daily or perhaps multiple times each day depending on size of the unit and how it is operated. Because of this daily turning and aeration, the composting process starts quicker and progresses faster in a rotary drum than with static-bin or alleyway composting; and the highly degradable, oxygen-demanding materials are decomposed in a shorter time frame than with other composting alternatives. Rotary drum composters, in general, all operate in a similar fashion to one another and offer additional advantages to traditional composting methods by being totally enclosed with less chance of escaping leachate, are quicker and more efficient at material breakdown due to daily turning and aeration, and use less added carbon source material, such as shavings or poultry litter.
Rotary drum composters have their origin in the swine industry. However, in recent years, the poultry industry has discovered the value of in-vessel composting to commercial poultry growers. Rotary composters are designed for large scale animal/poultry production facilities and offer the following benefits:
- Reduces odor and disease-causing organisms
- Eliminates the leaching threat and potential for soil and water contamination
- Removes animal decomposition from the public eye
- Enhances biosecurity by enclosing material and removing the scavenger threat
- Produces finished compost material that has value as a soil amendment
However, much like static bin or alleyway composting, rotary drum composters must have the proper working conditions if they are to perform as intended. Rotary drum composting requires that you follow a similar recipe to bin/alleyway composting to maintain adequate temperatures and moisture levels and achieve efficient composting results. Within the drum itself, the material must have:
- Adequate moisture content (50 to 60 percent)
- Oxygen (10 to 20 percent)
- Proper carbon-to-nitrogen (C:N) ratio (25-35:1 seems to work best)
- Enough carbon source or bulking agent (shavings, recycled compost, used litter, etc.)
- Correct amount of mortality (do not overload the unit; thereby upsetting the C:N ratio and decreasing the porosity)
The porosity (or amount of air space within the material) affects the availability of oxygen, temperature, microbial activity, composting time, and bulkiness and density of the material. It appears the porosity of compost material should be at least 35 percent to facilitate good air distribution and maintain optimum microbial growth. Moisture levels more than 60 percent should be avoided because moisture fills up air spaces within the material, increasing the bulkiness and density of the material and retarding aerobic activity, which reduces the temperature and increases composting time. In addition, too much moisture can result in the material becoming anaerobic which increases the likelihood of excess odor generation, decreased heating, and increased fly populations.
Carcass composting materials typically have mesophilic (grows best in moderate temperatures) and thermophilic (grows best at high temperatures) species of three groups of microorganisms, including: bacteria (present in largest numbers), fungi, and actinomycetes (gram positive bacteria that produce bioactive agents such as enzymes and vitamins) (Kalbasi et al., 2005). Bacteria are faster decomposers than other microbes and usually do well in the early stages of the composting process. Fungi do not do well in low-oxygen environments compared to bacteria but are better decaying agents on woody substrates such as shavings and are better able to withstand low moisture and low pH conditions. Critical to success is temperature, because nearly all microorganisms in compost material will die if the temperature rises above 158° F, leaving only a few heat-resistant spores. Therefore, it is important that the compost material get hot enough for the process to work efficiently, but not too hot.
Another useful feature of rotary drum composters is that they do their work out of the public eye. Public acceptance of agricultural practices is an important issue today that every farming operation must take seriously. Public acceptance of a rotary drum composter may be better simply because a drum composter may be more aesthetically pleasing than a bin or alleyway composter. In addition, scavengers are not a problem with a rotary drum composter because all the material is contained inside the drum, preventing scavenger access. With increased awareness of the threat of avian influenza, infectious laryngotracheitis, and other diseases, this can enhance a poultry farm’s biosecurity program.
Incineration
Mortality incineration is often used on pullet and/or breeder farms where mortality losses are less than on broiler farms. Incinerators use a fuel source (often propane) to burn the mortality so that all that is left is a dry ash product that must be manually removed from the incinerator. Smoke can sometimes be an environmental issue so choose a model that has an afterburner that burns the smoke to lessen the odor threat. The ash may contain small bits of bone but, for the most part, the entire bird is consumed. The ash is a concentrated source of potassium and phosphorus that is often mixed with poultry litter and land applied.
Choose a commercial grade incinerator that is well built. Even then, incinerators require maintenance because, over time, grates, blowers, and burners usually all need to be replaced. Make sure the unit is sized to the number of birds on the farm. If the incinerator is too small, this will mean multiple loadings and burnings throughout the day which can become quite labor intensive. Incinerators are small compared to bin/alleyway or rotary drum composters and should be strategically placed to avoid neighbors and take safety into consideration. Electrical and fuel access are required and placement on a concrete slab is advisable.
Freezing
On-farm freezer units have been an option in the past and are still an option in some locations, but freezers have lost some of their popularity due to avian influenza and biosecurity concerns. While the scavenger threat may be lessened with freezers, integrators are concerned that trucks picking up mortality often travel to many farms in a day, thereby increasing the potential for farm-to-farm disease spread and contamination. Freezer units are often required to be as far away as possible from the poultry houses. This may require the grower to invest additional money in remote sheds and electrical service to house and support the freezers.
Dehydration
The newest option for poultry growers to consider is a mortality dehydrator (Figure 6). Dehydration is currently approved in only a small number of states, but several states are considering the method. On-farm units are scaled-down versions of the technology used by large rendering plants to dehydrate and render mortality. They are sized based on the pounds of mortality they can handle in 12 hours. Calculate size (and perhaps number of units needed) based on estimated mortality and weight during the last week of the growout. Generally, the output is roughly 30 to 40 percent of the input.
Therefore, a unit sized for 1,300 pounds can handle 1,300 pounds of mortality twice in a 24-hour period. That’s 2,600 pounds of mortality dried down to roughly 40 percent, or 1,040 pounds of output in 24 hours. The units are designed for a one-time load during a 12-hour cycle. They cannot be shut down to load more mortality once a cycle has started. Like other daily mortality management options, dehydrators are not designed for excess mortality. Therefore, a secondary disposal option is advisable as a backup to handle periods of extreme mortality.
Dehydrators need to be under cover and have access to electricity. The finished product has reached sterilizing temperature, is dry with little odor, is safe to handle, and can be land applied like other compost materials. In addition, the scavenger and disease spread threat is eliminated because, like rotary drum composters and incinerators, dehydrators are a totally enclosed disposal system. Dehydrators use a 12-hour drying cycle which means a large amount of electricity is used. The significant electricity use and the initial unit and installation costs are current downsides to dehydration.
Summary
Mortality disposal is a critical daily management practice associated with commercial poultry production. This practice takes on greater importance today as more attention is focused on protecting the environment and the general public has more interest in agricultural practices, especially where livestock and waste management practices are concerned. Poultry growers have several options when it comes to mortality management. Composting is currently the most common method in use today. However, Brothers and Stanford (2022) conducted an economic analysis of poultry mortality disposal and found that, when all inputs and their costs are considered, the long-term costs per bird-day for all methods on their example farm were relatively similar. As a result, they indicated growers should consider other reasons for choosing one disposal method over another such as:
- How much time do I have to manage my mortality disposal method?
- Can my hired help manage my mortality disposal method correctly every day?
- Do I need to build and additional structure to house a method?
- Am I in an area where neighbor relations are more of an issue, and does that affect my choice of disposal options?
- How much longer do I plan to grow birds?
Mortality disposal is the grower’s responsibility and growers should check with their state agencies (environmental and agricultural) to be sure that they are in compliance with all mortality disposal regulations.
Additional detailed discussions of various poultry mortality management options can be found in subsequent factsheets in the Poultry Mortality Management section of the handbook.
References
Brothers, D., and K. Stanford. 2022. Mortality disposal methods for commercial poultry growers. Auburn University Publ. No. ANR-2921. August. https://www.aces.edu/blog/topics/farming/mortality-disposal-methods-for-commercial-poultry-growers/
Kalbasi, A., S. Mukhtar, S. E. Hawkins, and B. W. Auvermann. 2005. Carcass composting for management of farm mortalities: A review. Compost Sci. Util. 13(3):180-193. https://www.researchgate.net/publication/259332669_Carcass_Composting_for_Management_of_Farm_Mortalities_A_Review.
Tabler, T., J. R. Moyle, J. Wells, and M. Farnell. 2016. Composting poultry mortality: A critical daily management chore. Mississippi State University Extension Publ. No. 2960. June. http://extension.msstate.edu/sites/default/files/publications/publications/p2960_web.pdf.
Tabler, T., J. R. Moyle, and J. Wells. 2016. Rotary drum composting of poultry mortalities. Mississippi State University Extension Publ. No. 3012. November. http://extension.msstate.edu/sites/default/files/publications/publications/P3012_web.pdf.
Tabler, T., J. Wells, and N. Jefcoat. 2018. Composter operation and management. Mississippi State University Extension Publ. No. 3231. May. http://extension.msstate.edu/sites/default/files/publications/publications/P3231_web.pdf.