Poultry litter or layer manure is most often land applied to pastures and crops for its value as an organic fertilizer. Mortality, when properly composted, fits this category as well. We know from long experience how beneficial this practice can be when soil and manure nutrient testing are integrated with crop nutrient needs to determine the amount and timing of the application. This integration makes it possible to approach land application as a wise use of resources rather than as a disposal method.
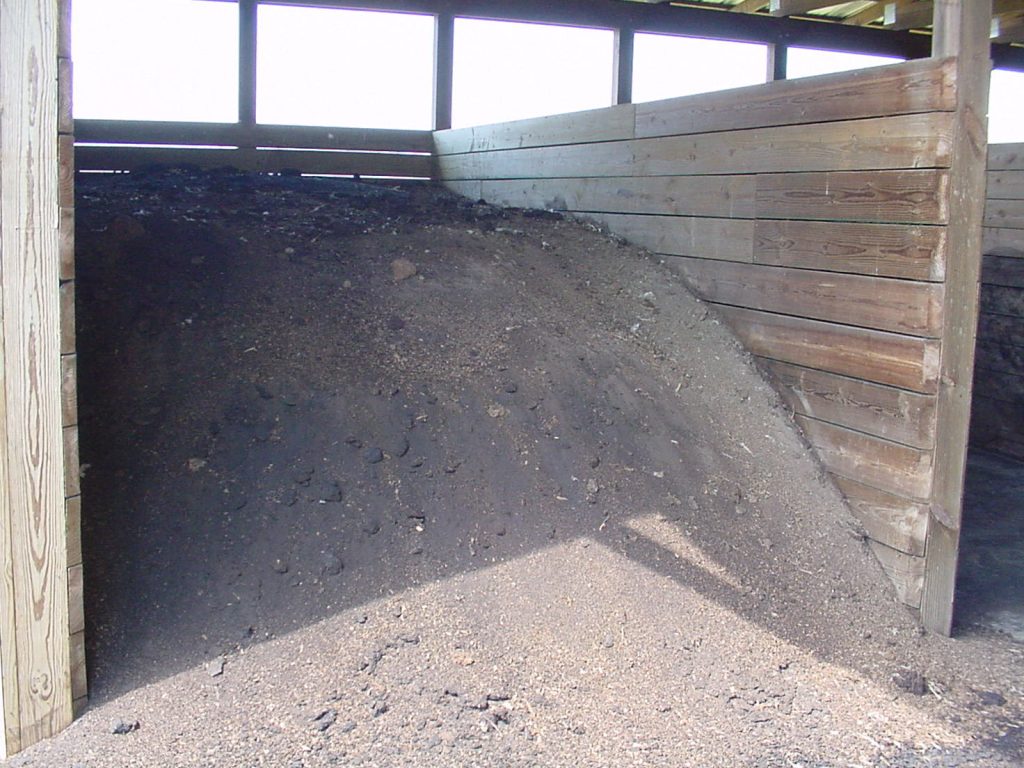
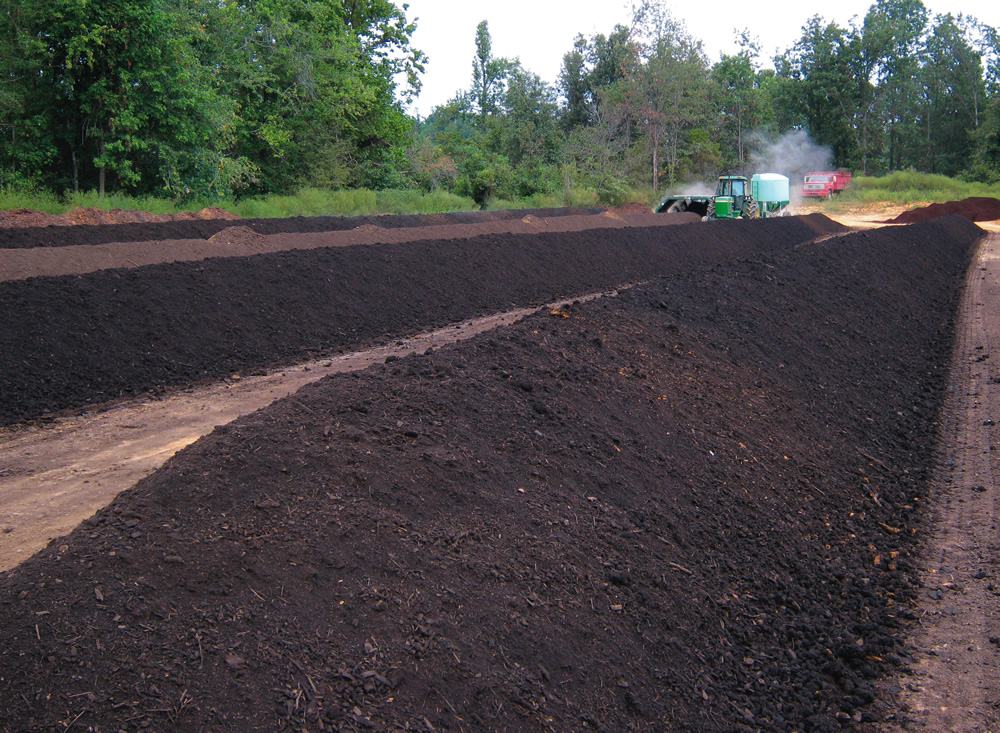
Proper storage and treatment of poultry co-products (litter, manure, hatchery waste, and dissolved air flotation [DAF] skimmings) before use are important to minimize compositional changes and decrease odor and handling problems. Depending on the co-product, dry storage, ensiling, or composting may be appropriate treatments. Resource management systems may include incineration and burial as methods of disposal; however, these techniques are not called treatments because they do not usually provide any reusable end products.
Composting is an environmentally sound and productive way to treat poultry co-products and mortalities (see also PMM/2 and PMM/3). The product of composting is easier to handle, has a smaller volume, and is a more stable product than the raw materials. The nutrient content of the compost will be nearly the same as the starting materials if the composting is performed properly.
While compost can be land applied to decrease the need for nutrients from commercial fertilizers, composted co-products may also be marketed for higher value uses on turf, for horticultural plant production, and in home gardening landscaping. It can be added as an amendment to soils for transplanting flowers, trees, and shrubs, or to establish new lawns. Compared to commercial fertilizers, poultry co-product compost will have a lower nutrient analysis (e.g., 2-2-2) for nitrogen, phosphorus, and potassium. However, there are other benefits to the soil and plant growth associated with the organic matter and micronutrients in compost.
Understanding the Process and Benefits of Composting
Composting is a natural, aerobic, microbiological process in which carbon dioxide, water, and heat are released from organic wastes to produce a stable material. Leaves and other organic debris are subject to this process all the time — that is, the activity of microorganisms transforms these materials into a soil-like, humus-rich product.
This natural process can also be used as a resource management technique to transform large quantities of litter, manure, and other poultry co-products into compost. The conditions under which natural composting occurs can be stimulated and controlled so that the materials compost faster and the nutrient value of the compost is maximized.
The composting process is relatively simple:
- Co-products, for example, litter, manure, egg shells, hatchery waste, and DAF skimmings, are placed in bins, piles, or elongated piles called windrows. A bulking agent or carbon amendment (e.g., sawdust, wood chips, yard waste, or paper that is rich in carbon but low in other nutrients) is usually necessary to provide the proper ratio of carbon to nitrogen in the mix and to improve aeration. The desired C:N ratio is 20-35:1.
- Air is needed to support and enhance microbial activity. Because the composting microorganisms are aerobic, that is, oxygen using, the windrows and compost piles must be aerated to ensure the efficiency of the process. Sufficient aeration also minimizes the formation of objectionable odors that form under anaerobic (oxygen depleted) conditions. Adequate aeration can be provided by forced air systems, such as blowers or fans; or by turning the compost with a front-end loader or a commercial compost turner.
- Mechanical agitation or turning of the materials supplies aeration, helps mix the materials, and distributes any added water.
- Temperatures in the compost must be maintained at levels above approximately 131°F to kill any pathogens (disease-causing organisms) and promote efficient composting. Temperatures above 160 to 170°F should be avoided because they reduce the microorganisms that are beneficial to the composting process. Turning the materials can regulate temperature.
- Adequate moisture, between 40 and 60 percent, is necessary for optimal microbial activity.
- To assure good composting, the pH should be between 6.5 and 7.5.
Handling Compost
Compost produced from poultry co-products can be used in many different ways: it can be used directly as a soil amendment for agricultural or horticultural uses; pelletized or granulated for ease of transportation and application; or enhanced with conventional fertilizers to improve its nutrient value.
Possible Drawbacks
Composting, like any management technique, cannot be undertaken lightly, whatever its benefits. It requires a commitment of time and money for equipment, land, storage facilities, labor, and management. Composting is an inexact process that depends heavily on the quality and characteristics of the materials being composted and the attention given to the composting process.
Although the finished product should have no odor or pest problems, such problems may occur during the composting process. Weather may also affect the process adversely. Compost releases nutrients slowly — as little as 15 percent of the nitrogen in compost may be available during the first year of application. In addition, costs associated with production-scale composting can be significant, and federal and state regulations for stormwater runoff from the composting site must be followed.
Despite these potential drawbacks, composting on the farm is a practical resource management technique. Good management will consider every opportunity to eliminate or reduce the concerns associated maximizing its benefits. Once it is realized that composting can be more than a “dump it out back and forget it” procedure, the technique can be used and adjusted to meet co-product management needs.
Composting Methods
There are four general methods of composting: passive composting, windrows, aerated piles, and in-vessel composting.
Passive Composting
Passive composting is the simplest, lowest cost method. It requires little or no management because the materials to be composted are simply stacked into piles and left to decompose naturally over a long time.
Passive composting is not suitable for the large quantities of litter or manure produced on poultry farms. It occurs at comparatively low temperatures and decomposition occurs at a slow rate. Anaerobic conditions resulting from insufficient aeration can result in objectionable odors.
Windrow Composting
Windrow composting occurs in long narrow piles that can vary in height and width depending on the materials needed for proper composting.
For most efficient composting, windrows are turned as required depending on temperatures at both 12″ and core depth (approximately 36″) of the windrows.
Windrow composting (Fig. 1) is usually well suited to poultry farms if sufficient space is available. In this method, the windrows are formed from the material to be composted, water, and any bulking agent. The piles can range with composting while from 3 feet high for dense materials to as high as 12 feet for lighter, more porous materials like leaves. If the piles are too large, anaerobic conditions can occur in the middle; if they are too small, insufficient heat will be maintained for pathogen reduction and optimum microbial activity.
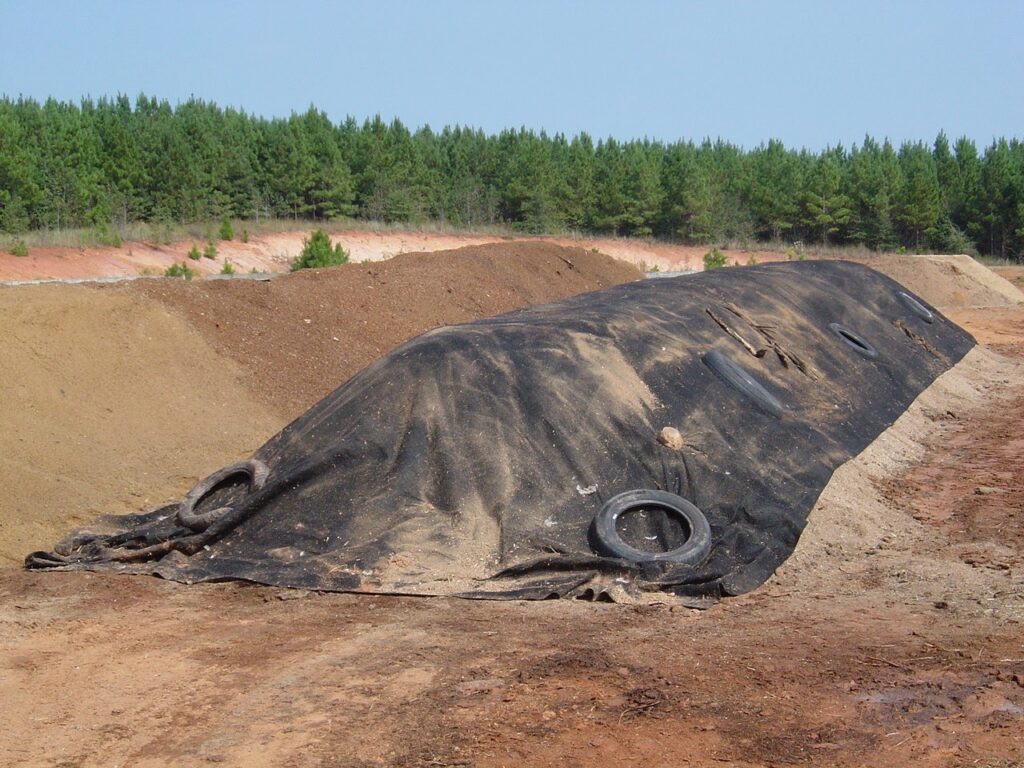
The windrows are turned periodically to add oxygen for microbial growth, mix the materials, rebuild porosity (as the mixture settles), release excess heat, and expose all materials equally to the high interior heat that kills pathogens. Turning can be labor and equipment intensive depending on the method used. In the beginning, it may be necessary to turn daily or even several times a day to maintain sufficient oxygen levels; however, turning frequency declines with the windrow’s age.
In addition to needing space for the windrows, the producer will also need turning equipment, a source of water, a dial thermometer, and perhaps an oxygen meter. The turning equipment (Fig. 2) can be front-end loaders, manure spreaders with flails and augers to provide good mixing, or specialty machines. Often older, unused farm equipment, for example, an old potato plow and a farm tractor, can be used for turning compost.
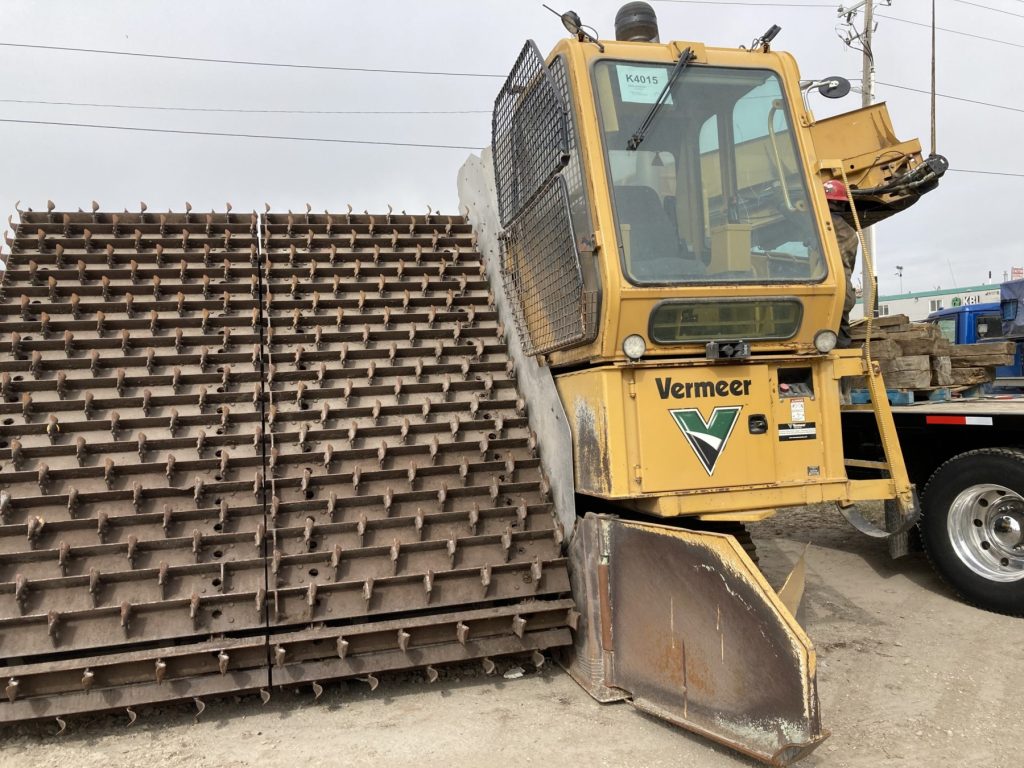
Temperatures within the windrow are most commonly used to determine when turning is necessary. Low temperatures and odors are signs that more oxygen is needed, while cool or hot spots at intervals along the windrow indicate that the material needs to be mixed. During fly season, all windrows should be turned at least weekly. In the winter, windrows can be combined to conserve heat as they diminish in height. Composting time can vary from weeks to months depending on the material being composted, the attention given to composting conditions, and the quantity of material composted.
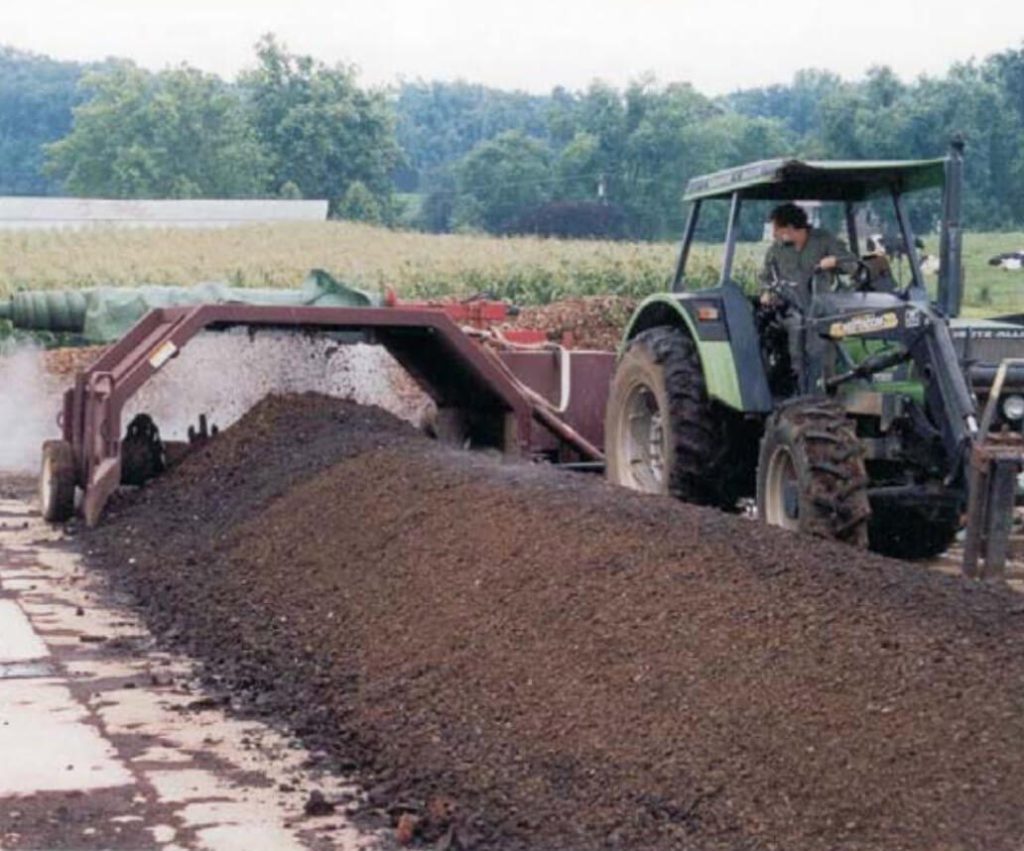
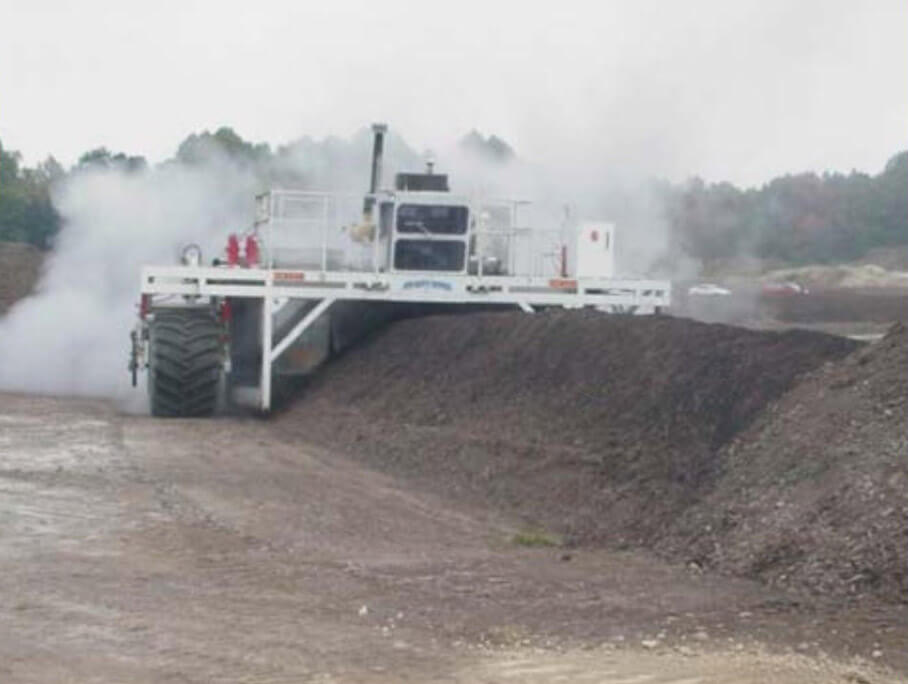
Aerated static
Aerated static composting eliminates the labor of turning the compost by using perforated pipes to introduce air into piles or windrows.
Air can be supplied with blowers to force air into or through the composting material.
Passively aerated windrows (Fig. 3) are a modification of windrow composting that eliminates turning. In a commonly used system, the windrow is placed on a base of wood chips, straw, or peat, and perforated aeration pipes are added on top of this base. The material to be composted must be very well mixed, since it is not turned, and the windrow should not be higher than 3 to 4 feet. This method has the advantage of minimizing odors and helping to conserve nitrogen.
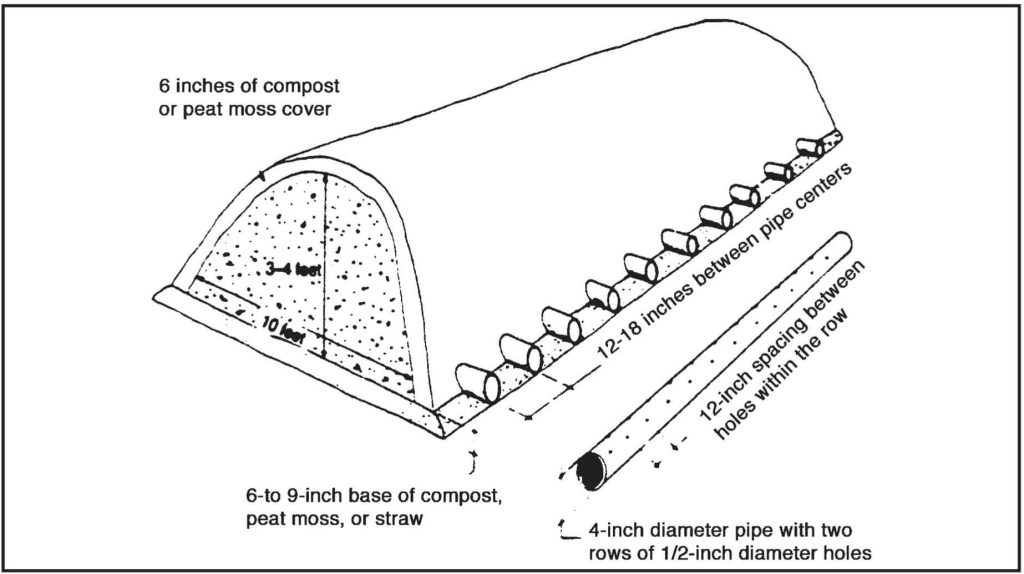
This diagram shows a windrow with a 6-9 inch base of compost, peat moss, or straw. Perforated aeration pipes are added on top of base with 12-18 inches between pipe centers. Each pipe is 4 inches in diameter with two rows of 1/2 inch diameter holes, with 12 inch spacing between holes. The windrow is covered in a 6 inch layer of compost or peat moss. Aerated static piles or windrows add blowers to the aeration pipes. This method allows for larger piles or windrows and permits more efficient composting than passively aerated static piles. Air can either be drawn into or forced through the composting material. The blowers may be controlled to turn on at set intervals or in response to temperatures in the pile or windrow.
In-vessel composting
In-vessel composting is similar to aerated methods but the materials to be composted are contained in bins or reactors that allow for control of aeration, temperature, and mixing, in some systems.
In-vessel composting is actually a combination of methods that involve both aeration and turning. Mixing can be optimized, aeration enhanced, and temperature control improved.
The simplest form of in-vessel composting is bin composting, which is readily adaptable to poultry farms. Bins may be plain structures with a roof, conventional grain bins, or bulk storage buildings. Other types of in-vessel composters use silos in which the air goes in at the bottom and the exhaust is captured for odor control at the top; agitated bed systems; and rotating drums. Costs for equipment, operation, and maintenance for a large quantity of materials are high for in-vessel composting.
Factors to consider in choosing a composting method are speed, labor, and costs. Windrows are common on farms; they can use existing equipment, no electricity is required (so they can be remotely located), and they produce a more uniform product. They are, however, also labor intensive and at the mercy of the weather. Adding a paved or compacted clay surface and a simple open-sided building can minimize weather problems and the impact of composting on water quality.
For more information, technical assistance, and possible cost-share programs that may be available to help you begin a composting operation, contact your local conservation district office, the USDA Natural Resources Conservation Service, or the Cooperative State Research, Extension, and Education Service.
References
Biocycle. 1991. The Art and Science of Composting. The JG Press, Inc., Emmaus, PA.
Cabe Associates, Inc. 1991. Poultry Manure Storage and Process: Alternatives Evaluation. Final Report. Project
Number 100-286. University of Delaware Research and Education Center, Georgetown.
Carr, L.E. 1997. Composting Poultry Litter. Congressional Animal Waste Conference. Longworth House Office Building, Washington, DC
Carr, L.E., R.C. Moore, and C.A. Johnson. 1992. Composting Dissolved Air Flotation Skimmings from Poultry Proceessing. ASAE Paper 92-6016. International Summer Meeting of the American Society of Agricultural Engineers, Charlotte, NC.
––––––. 1992. Hatchery Waste Composting. Pages 139–144 in Proceeding of the 1992 National Poultry Waste Management Symposium. Sheraton Civic Center Hotel, Birmingham, AL. ISBN 0-9627682-6-3.
Donald, J.O., C.C. Mitchell, and C.H. Gilliam. 1990. Composting Agricultural Wastes in Alabama. ANR Circular 572. Cooperative Extension Service, Auburn University, Auburn, AL.
Rynk, R., ed. 1992. On-farm Composting Handbook. NRAES-54. Cooperative Extension. Northeast Regional Agricultural Engineering Service. Ithaca, NY.
Smith, B. 1993. Composting and Uses for Manure. Presentation. 1993 Waste Management and Water Quality Workshop. Southeastern Poultry and Egg Association, Atlanta, GA.